I finished the tank top mould yesterday and once it was cured had to separate it from the stand it was on.
Up until the tank mould I have been using Easy Composites for all the CF and GF resin and matting supplies. It is good stuff but EC are at the top end of the market for price. Their polyester resin is sea water green and translucent and quite viscous, think EP90. I shopped around for polyester resin and bought some cheaper stuff which is cream coloured and much less viscous, think 10W fork oil. Aside from the price benefit it is much easier to wet the glass mat and seems better at resisting the formation of air pockets when stippling the resin. The downside is that it runs everywhere and on the tank mould with near vertical sides resin puddles formed naturally at the bottom of the tank sides at the junction with the base board. It took about 2 hours with a wood chisel to separate the mould from the base.
From a cursory inspection (and without separating the three parts of the top mould) it looks as though the tank top mould has come out well with the flanges nice and flat and well defined. I also think that the tank bottom mould can be done as one piece.
Picture below shows mould just as I turned it over with all the debris from releasing it still in it
exxon station near me
What has become evident though is that my original planned scheme to bond the tank top to the bottom will not work. If I had thought about it for more than a nano-second then it was blindingly obvious that it would never have worked as when the two halves are introduced to each other there will be a very fine single point of contact between them which will not bode well for either strength or juice retention capability.
It is clear that I will have to form a “ledge” about 10 to 20mm wide on the inside of the tank top marrying accurately with the profile of the tank bottom about 5mm above the bottom edge of the tank. When the tank bottom is formed it will have to be cut about 0.5mm undersize so that it fits inside the tank top and sits comfortably and consistently on this ledge. This is not going to be easy and as I sit now I have no real clue as to how to do it. The underside of the tank at the junction with the tank top along both flanks is semi-circular to accommodate fitting over the frame rails, it is only at the front and back that a right angled “ledge” is possible.
The other possibility is to mould the tank bottom and form an “up stand” all around the base mould that marries with the profile of the inside of tank top.
On balance the “ledge” appears a better solution as it will be easier to ensure that contact between the two halves is complete and that resin contact between them is continuous but forming it accurately along the edge of the underside of the tank top will be a significant challenge.
The hump part of the seat mould is now complete and a first gel coat has been applied to the seat part.
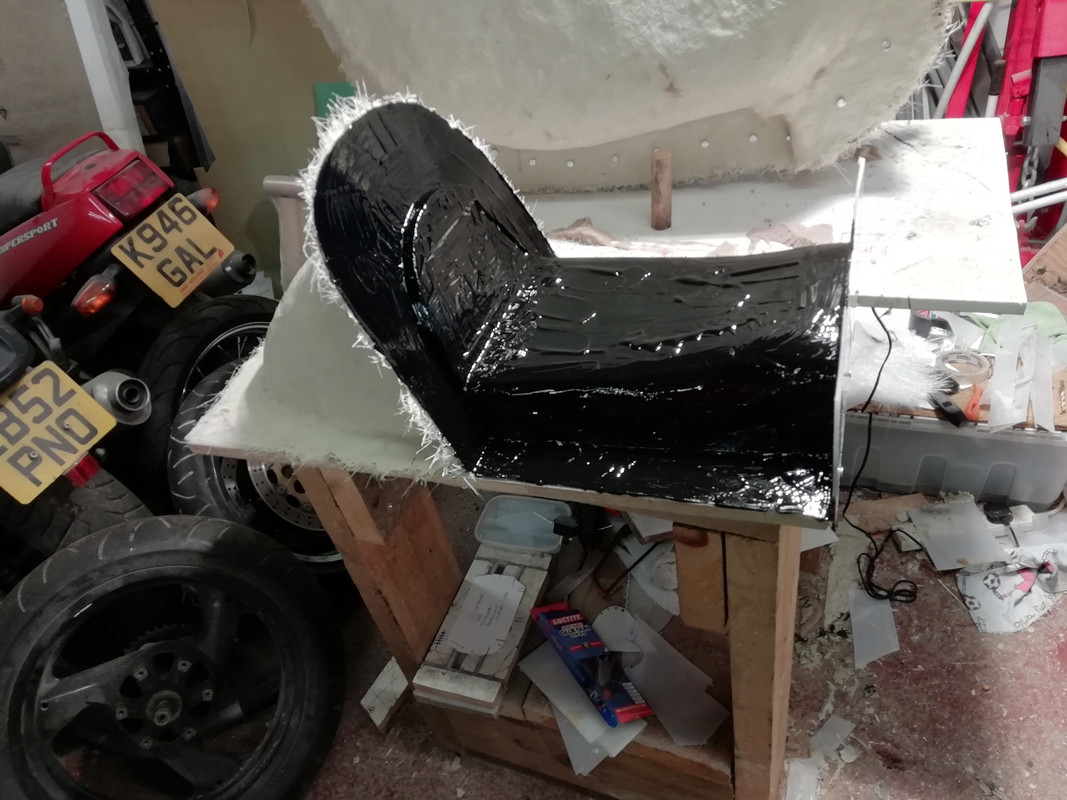
Work continues with cutting cotton patterns for the CF to go into the moulds